What Is Reverse Engineering?
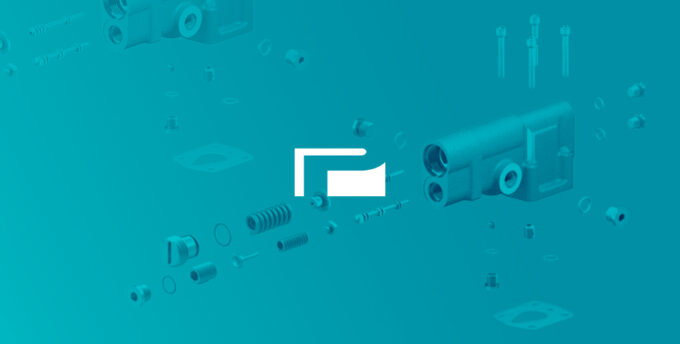
Manufacturers like Panagon Systems rely on reverse engineering to ensure quality.
Reverse engineering is the process of identifying a product’s design as it was originally manufactured. It is called reverse engineering because you start the process with an already-manufactured product and end it with design blueprints. Reverse engineering is a less costly and often faster solution than buying replacement parts. Furthermore, reverse engineering is needed when a part is obsolete or discontinued.
Let’s take a closer look at how the process works.
The Reverse Engineering Process
The reverse engineering process varies depending on the product, object, or software being inspected.
In this post, we’ll focus on the process of reverse engineering a hydraulic pump.
The first step of reverse engineering a pump involves inspection, testing, and data collection. The engineer needs to know everything possible about the pump, including its weight, dimensions, mounting capabilities, maximum operating pressure, maximum operating speed, and more. An engineer may use a coordinate measuring machine (CMM) or a 3D scanning system to measure the component accurately.
Then, the engineer will create a general three-dimensional sketch of the pump using computer-aided design software.
Once the sketch has been created, the engineer will disassemble the pump and inspect, test, and measure each component. During the disassembly process, it’s likely that the engineer will also take note of any components that could be added or removed in the final design based on the client’s request (lower overhead costs, better efficiency, etc.).
The engineers will then create a general blueprint of what the product should look like, reassemble the pump, and test it to ensure quality.
Reverse Engineering Benefits
- Fix Outdated Systems: If you need to repair your hydraulics system, you may find that some parts are no longer manufactured. In these instances, reverse engineering is the only way to repair obsolete equipment pieces and get operations up and running again.
- Reduce Costs: Making a new component by reverse engineering is affordable and convenient, especially when dealing with obsolete or discontinued products.
- Improve Design: Many manufacturers require customized machinery to accomplish specialized or complex applications. With reverse engineering, you can improve on an existing design or develop a more efficient design variation. The re-engineering process may also help improve system performance, timing, or safety.
- Missing Documentation: Most customized pieces of machinery come with documentation or blueprints. Some blueprints are delivered outdated or incomplete, and it is common to misplace them after a few months. Doing reverse engineering on the machinery can help you recreate or improve these documents.
Learn More About Reverse Engineering Today
Panagon Systems is an industry-leading manufacturer of aftermarket hydraulic piston pumps and motors. We utilize reverse engineering to ensure OEM quality of all pumps, motors, and parts we produce. Contact us today to learn more about our replacement pumps and motors.